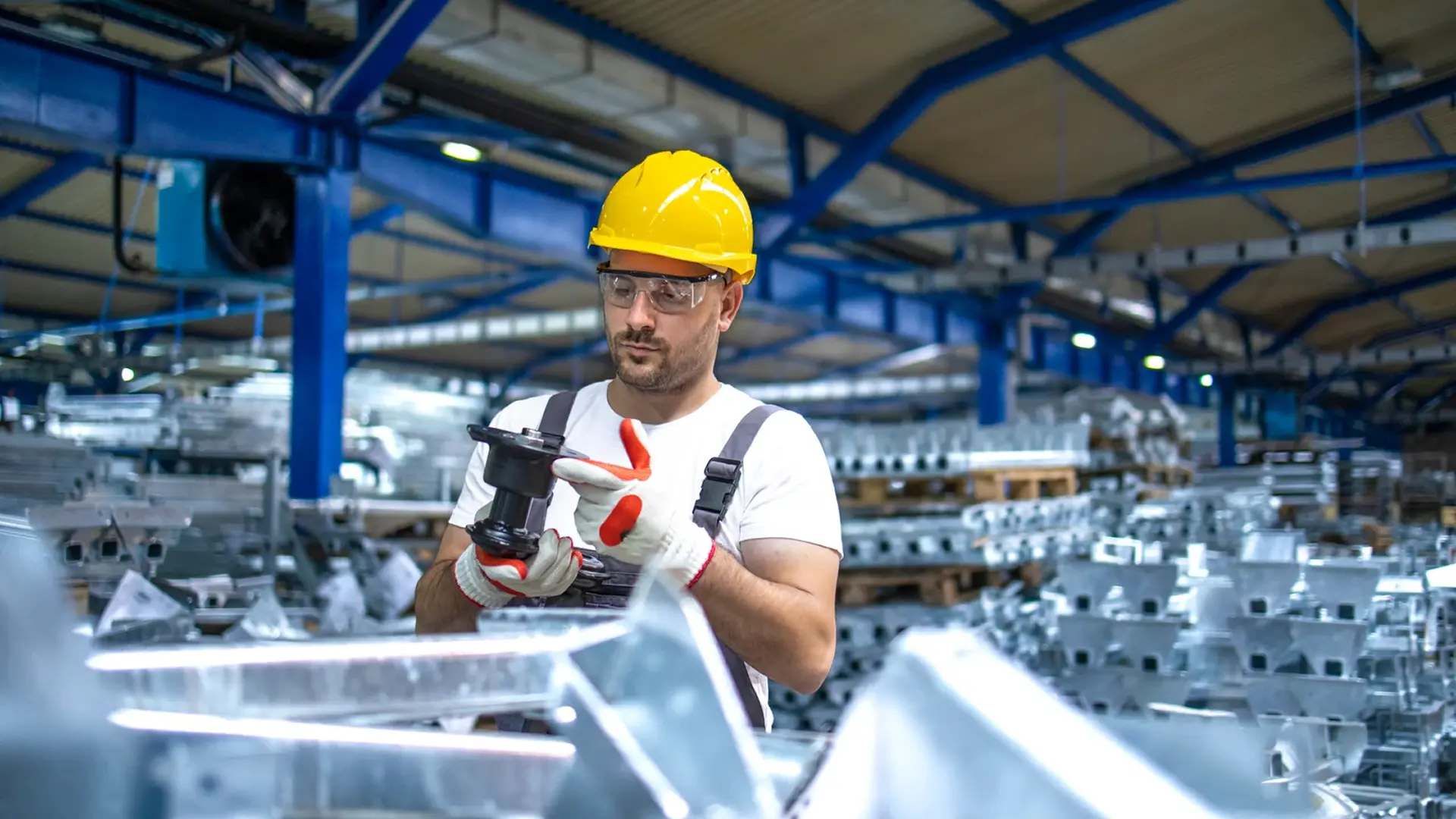
Key Takeaways
- Computer vision enables automated, real-time tracking of warehouse inventory, reducing dependency on manual processes and minimizing errors caused by human intervention.
- The architecture relies on cameras, sensors, and AI to capture, process, and analyze visual data, improving the efficiency of inventory control.
- Preprocessing steps like image enhancement and noise reduction ensure the AI system works with high-quality, relevant visual data.
- AI models such as CNNs, YOLO, and OCR accurately recognize, classify, and extract information about warehouse items and product movement.
- Integration with WMS/ERP systems and a user-friendly UI ensures real-time synchronization, actionable alerts, and clear visibility for warehouse staff.
Fulfilling customer needs is an essential factor for manufacturing enterprises to grow. Additionally, they should offer top-notch products at reasonable prices. A minor defect or low-quality products can damage your company’s reputation. Customers tend to leave testimonials and reviews, which impact a company’s success. Henceforth, every manufacturer should prioritize quality control and ensure customer satisfaction.
Traditional QC systems utilize basic machines and human inspectors with proper guidelines. For example, an employee may identify every product to check for defects and determine whether it is the right size. Rule-based machines may not be able to detect all the problems, especially if they are hidden. This is where multimodal generative AI can work. It is an innovative and modern way to improve the manufacturing industry’s prioritization of quality.
Also read: AI Agents for Regulatory Compliance Monitoring in Banking.
What Is Multimodal Generative AI?
Let’s understand the words one by one.
Multimodal means the AI can examine and understand different kinds of information simultaneously. For example, it can explore pictures and videos of products, read text reports, listen to machine sounds, or check signals from factory sensors. Instead of focusing on just one data type, it can combine many types to understand better.
Generative AI is an artificial intelligence that learns from large amounts of data and can create new data, make predictions, or offer innovative suggestions. It doesn’t just follow fixed rules—it learns patterns and can make decisions like a human expert.
So, Multimodal Generative AI means using a smart AI that can take in lots of different types of data and use that to understand if something is wrong with a product, predict when a machine might fail, and even suggest how to fix a problem.
For example, if a machine in the factory makes a strange noise and the product it makes has a tiny defect in its shape, the AI can listen to the sound, look at the product’s image, and read sensor data. Then, it can figure out what went wrong and alert the staff—much faster and more accurately than a human might.
This kind of AI helps factories save time, reduce waste, and make better-quality products, which benefits both companies and customers.
Why Does Quality Control Need Multimodal AI?
Quality Control (QC) is significant in manufacturing because it helps ensure that every product is safe, correct, and works as expected. However, the traditional quality control methods are not always good enough, especially when products or machines become more complex. The current QC methods face several challenges that make it hard to catch every problem on time.
One of the most common QC methods is visual inspection. This means a person or a camera looks at the product to check for defects like scratches, cracks, or missing parts. However, human workers can tire, especially when checking hundreds or thousands of products daily. They may miss tiny defects or get distracted. Even cameras, better than humans in some ways, can still miss defects if the rules are too simple or don’t cover all types of problems.
Another method is sensor data analysis. Factory machines often have sensors that collect data like temperature, pressure, speed, or vibration. These sensors help detect when something is going wrong. However, traditional systems usually work according to fixed rules. For example, an alarm goes off if the temperature exceeds a set number. The problem is that not all issues follow explicit rules. Some failures are hard to predict with simple logic, so that these systems may miss them.
Then there are text reports or manual entries written by workers or engineers. These include notes about issues, maintenance work, or quality checks. Reading and understanding all these reports takes a lot of time, and people can make mistakes or forget to report essential things.
Factories also produce audio signals, like the sound of machines running. Sometimes, strange noises mean a problem is starting. But most traditional systems don’t even listen to these sounds, or they look at them separately, not as part of the whole picture.
This is why Multimodal Generative AI is a game-changer. It can take in all of these data types—images, sensor data, text, and sound—at the same time and understand patterns across them. This helps it find problems faster, whether complex or new. It can also suggest what might be causing the problem and how to fix it.
By bringing everything together, Multimodal AI makes quality control much more innovative and reliable.
How Multimodal AI Works in a Production Line?
Multimodal AI is an innovative technology that helps factories accurately and quickly check product quality. It works step by step, starting with data collection and ending with decisions to improve the production process. Let’s look at how it works simply.
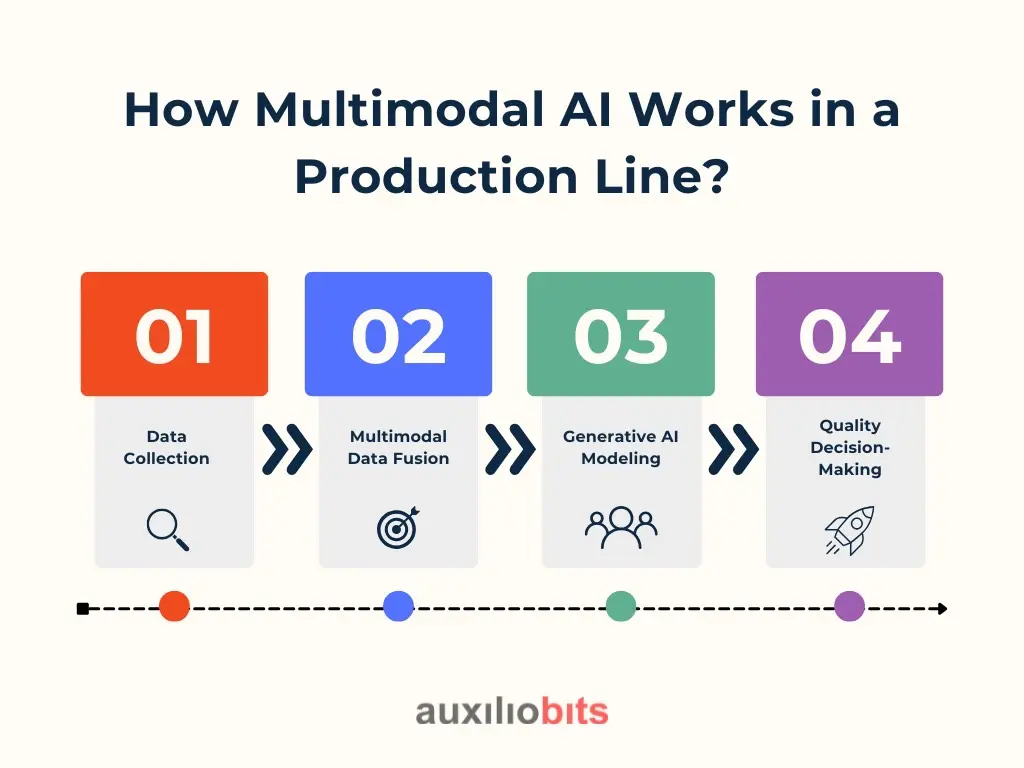
1. Data Collection
The first step is collecting different types of data from the production line. This includes:
- Images and videos taken by cameras that watch the products as they move on the line show the outside of the product to check for cracks, scratches, or wrong shapes.
- Sensor data from machines, such as temperature, pressure, speed, or vibration, tells us how the machines work and whether something unusual is happening inside.
- Text data, such as logs, error messages, and notes entered by workers or engineers. These often contain clues about what went wrong or when something was fixed.
- Audio data, like the sounds made by machines, motors, or conveyors. Strange sounds often mean a part may wear out or something is about to break.
All this data is collected continuously and in real time as products are being made.
2. Multimodal Data Fusion
Next, the AI system combines all this information. This is called data fusion. Instead of looking at each data type separately, the AI connects the dots. For example, it might match a strange noise with a drop in pressure and a blurry product image. Combining everything gives the AI a full 360-degree view of the product and the process.
3. Generative AI Modeling
Now, the AI learns from this combined data. It studies past production runs, learns what normal behavior looks like, and remembers what kinds of problems have happened before. This learning helps the AI make predictions, spot unusual patterns, and even simulate future issues before they occur.
For example, it might predict that a machine is about to fail based on a change in sound and pressure, even before a defect shows up in the product.
4. Quality Decision-Making
Finally, the AI uses this knowledge to make decisions:
- It checks if a product is good or defective.
- It figures out why a defect happened.
- It alerts the team or, in smart factories, automatically adjusts machine settings to fix the issue right away.
This whole process helps factories make better products faster and with fewer errors.
Benefits of Using Multimodal Generative AI
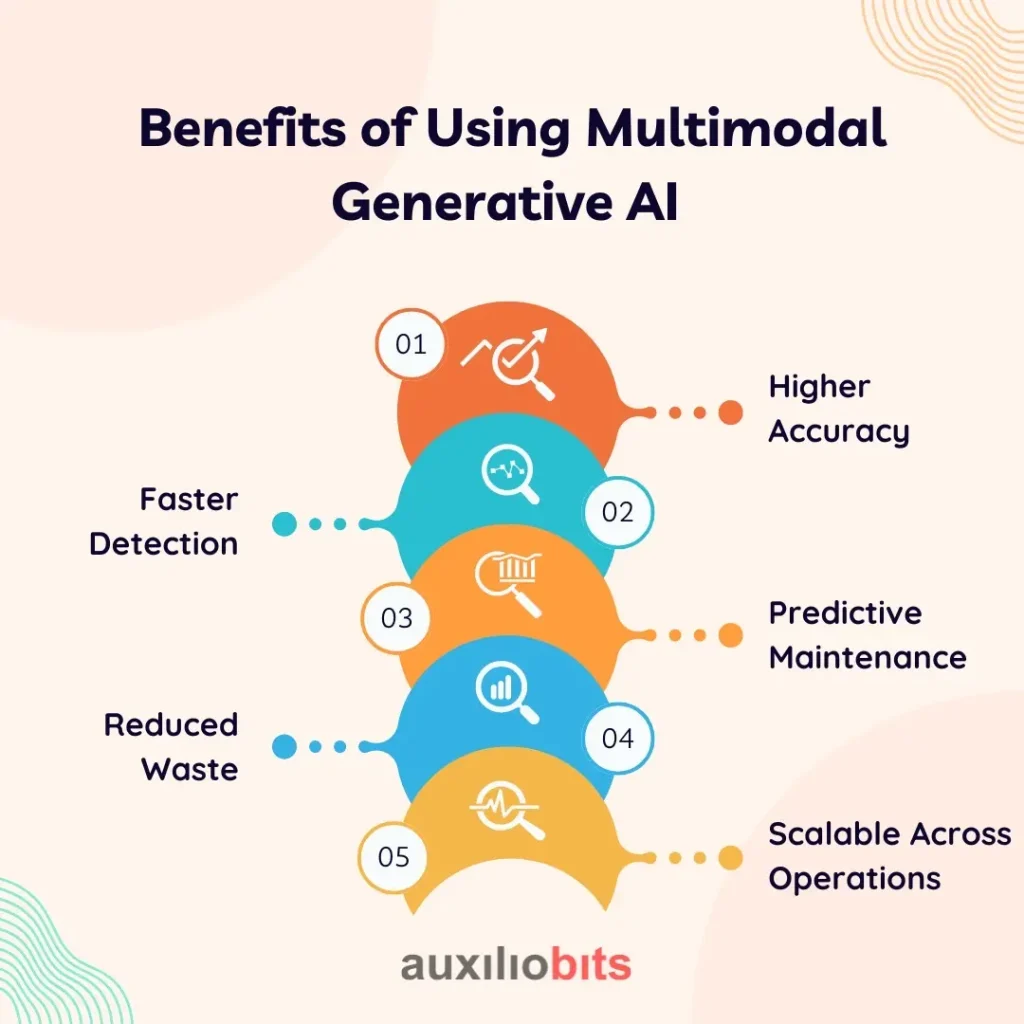
Using Multimodal Generative AI in manufacturing brings many powerful benefits. It helps factories improve product quality, reduce costs, and become more efficient. Let’s look at the main advantages simply.
1. Higher Accuracy
One of the most significant benefits is better accuracy in finding defects. Traditional systems might only look at one data type, like an image or a sensor reading. However, multimodal AI looks at many data types, such as images, sound, sensor data, and text. This gives the AI a deeper understanding of what’s happening. It can catch even small or hidden problems that humans or simple machines might miss. This means more reliable quality checks and fewer defective products going out to customers.
2. Faster Detection
Multimodal AI works in real time. This means it can spot problems as soon as they happen, instead of waiting until the end of the production line. When something looks wrong—maybe a machine is making a strange noise or a product seems slightly off—the AI can immediately send an alert. This helps workers quickly stop the issue before it becomes bigger.
3. Predictive Maintenance
Multimodal AI doesn’t just react to problems—it can predict them before they happen. By learning from past data, the AI can tell when a machine is starting to behave differently, even if it hasn’t broken yet. This allows the factory to do predictive maintenance, such as fixing or cleaning a machine before it causes defects. This reduces downtime and avoids surprise breakdowns during busy production hours.
4. Reduced Waste
Fewer defective products are made when problems are caught early and machines are kept in good shape. This means there’s less rework (fixing bad products) and less scrap (throwing away damaged goods). Over time, this significantly saves materials, energy, and labor. It’s also better for the environment.
5. Scalable Across Operations
Multimodal AI systems are scalable, which means they can simultaneously be used across many machines, lines, or factories. The same knowledge can be applied elsewhere once the AI learns to check quality in one area. This makes it easy for companies to grow and maintain high quality, no matter how big they get.
Tools and Technologies Involved
- Vision Models: Detect surface defects from images/videos (e.g., YOLO, Segment Anything Model)
- Sensor Analytics: Understand patterns from IoT data
- Audio Recognition: Analyze sounds using deep learning (like CNNs for spectrograms)
- Multimodal Transformers: Models like CLIP or FLAVA can merge different data types
- Edge AI + Cloud: Run models close to machines and sync with the cloud for training and updates
Conclusion
Multimodal Generative AI is not just another automation tool—it’s a game-changer for quality control. By combining vision, sound, sensor, and text data, it gives manufacturers the power to:
- Catch defects faster
- Reduce costs
- Improve product quality
- And stay ahead in a competitive market.
As technology matures, now is the perfect time for manufacturers to explore and adopt innovative systems on their production lines.