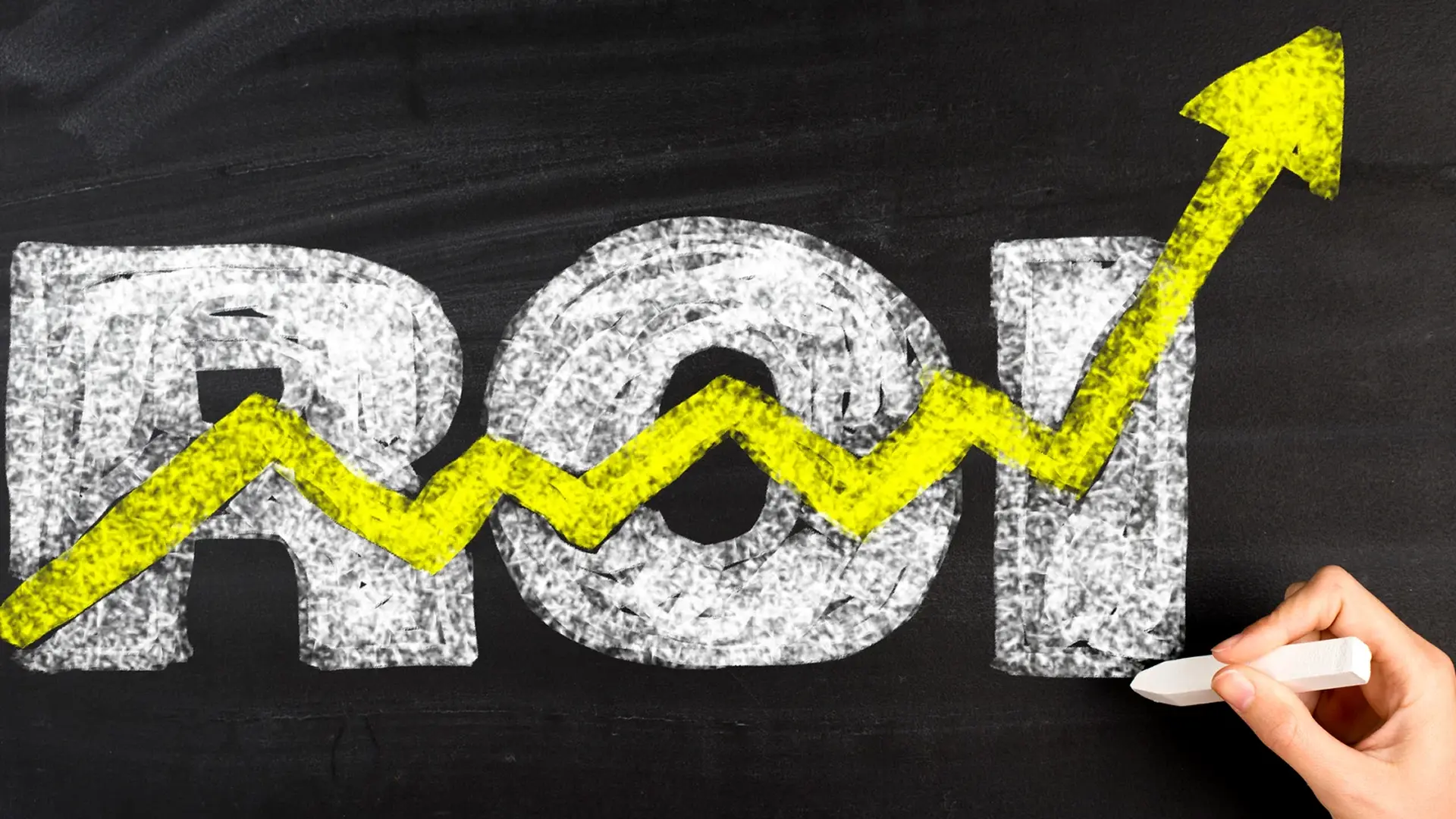
Key Takeaways
- AI optimizes energy use by learning usage patterns and automating smarter decisions, reducing waste, and improving factory efficiency.
- Traditional factories often waste energy due to idle machines, poor scheduling, and hidden faults—AI helps fix these issues in real time.
- AI-driven systems collect sensor data, analyze it, and either suggest improvements or take automatic actions to cut energy use.
- ROI from AI-powered energy optimization is measurable, often paying off within a year through reduced costs and higher operational efficiency.
- Starting with an audit and gradually scaling AI with sensors and pilot tests ensures a smooth, cost-effective implementation in manufacturing plants.
In today’s world, energy costs are rising and sustainability is becoming more critical. Manufacturing companies seek more innovative ways to reduce energy use, lower costs, and help the environment. One powerful solution is AI-powered energy optimization. This blog will explain what it means, how it works, and how it brings a strong return on investment (ROI).
What Is AI-Powered Energy Optimization?
AI-powered energy optimization uses artificial intelligence to improve energy use in a manufacturing facility. It goes beyond traditional energy management systems that only track energy consumption. AI helps factories become smarter by learning how, when, and where energy is used. It then uses this knowledge to find better ways to use energy, reduce waste, and save money.
AI systems collect data from sensors and machines across the facility and analyze it in real time to understand usage patterns. For example, AI can see when specific machines use more energy or when energy demand is highest during the day. It can also detect when equipment is running inefficiently or might be about to fail.
One of AI’s biggest advantages is its ability to predict the future. It can forecast energy needs for the coming hours, days, or weeks based on past data. This helps factories prepare in advance, reducing peak energy loads and avoiding costly downtime. Instead of reacting to energy issues after they happen, AI allows teams to act before problems occur.
AI can also automatically adjust energy use to optimize it. For instance, it might lower power to non-essential machines during peak hours or shift energy-heavy tasks to times when electricity is cheaper. This process, called “demand response,” helps reduce energy bills and strain on the grid.
In short, AI-powered energy optimization helps manufacturing plants become more efficient, reliable, and sustainable. It supports cost savings, lowers carbon emissions, and ensures smooth operations. By combining data, predictions, and automation, AI transforms how factories manage energy, not just by watching it, but by actively improving it every second.
Also read: EMR Integration Using LangChain and OpenAI for Smart Data Entry
Why Is Energy Optimization Important in Manufacturing?
Manufacturing plants use a large amount of energy every day. They need power to run machines, lights, heating, ventilation, air conditioning (HVAC), and many other systems. Energy is one of the most significant costs in manufacturing. When energy is used poorly or wasted, it affects the company’s profits and the environment.
Many factories use more energy than they need. This happens for several reasons. Sometimes, machines keep running even when they are not in use. For example, a motor may stay on during lunch breaks or overnight. This wastes electricity and adds unnecessary wear and tear to the equipment.
Another common problem is poor temperature control. HVAC systems may overheat a space, especially in large factories. If the temperature is not set correctly, energy is wasted while workers are uncomfortable. This can lower productivity and increase energy bills.
Production schedules can also cause energy waste. If tasks are not planned efficiently, machines may be turned on and off too often or run at full power when not needed. Unplanned downtime, last-minute changes, and poor coordination between departments can all lead to unnecessary energy use.
Hidden faults in equipment are another major issue. Sometimes, a machine works fine but is using more power than usual. These issues are complex to detect without advanced monitoring tools. Over time, these minor problems add up to significant losses.
Energy waste increases operational costs and the factory’s carbon footprint, harming the environment. Energy efficiency has become more critical as more governments and customers demand greener practices.
AI-powered energy optimization helps solve all these problems. AI can monitor all energy use in real time. It finds where waste is happening, predicts future needs, and suggests or makes changes automatically. It learns patterns and improves over time.
Using AI for energy optimization, factories can cut costs, reduce emissions, and operate more efficiently. This helps them become more sustainable, stay competitive, and meet environmental goals. In today’s world, smart energy use is not just good practice—it’s a necessity for modern manufacturing.
How Does AI Optimize Energy in a Factory?
AI-powered energy optimization in a factory works by collecting data, analyzing it to find patterns, and then making smart decisions or actions to improve energy use. Let’s break this down step by step in a simple way.
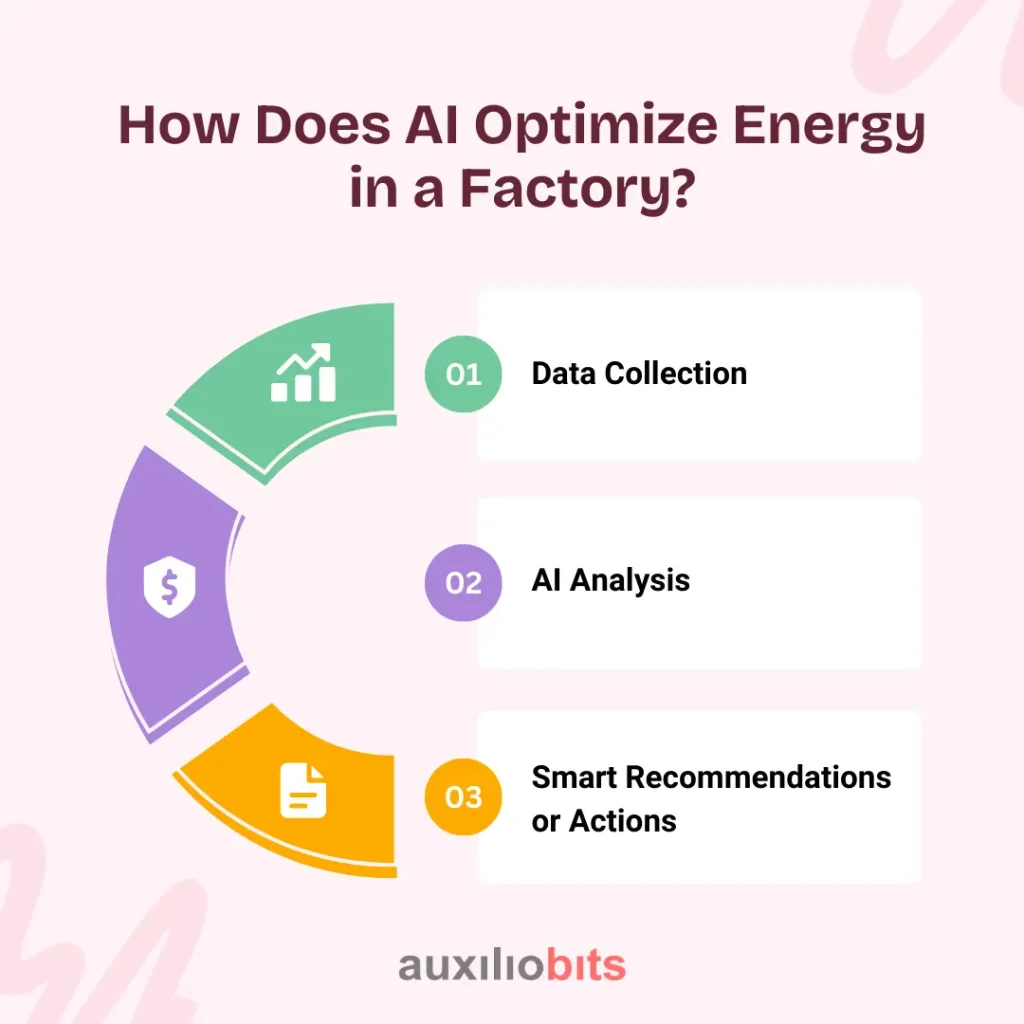
1. Data Collection
The first step is to gather information. Sensors are installed all around the factory. These sensors constantly monitor and collect data in real time. Some of the key things they track include:
- Power usage: How much electricity each machine or system uses.
- Machine performance: Whether machines run efficiently or use more power than usual.
- Temperature and humidity: The indoor climate in different parts of the factory.
- Production schedules: When machines are operating and when different tasks are happening.
This data provides a clear, detailed view of everything inside the factory. It helps AI “see” the entire energy flow across the facility.
2. AI Analysis
Once the data is collected, AI software analyzes it. The goal is to find patterns and detect where energy is being used well and where it’s being wasted.
For example, AI might notice:
- A machine always uses more energy in the afternoon, possibly due to wear, heat, or increased workload.
- The air conditioning continues to run at full power even during night shifts when no one is in the building.
- Some shifts or teams use more energy than others, even though they do the same work.
AI doesn’t just look at one day—it seems at weeks or months of data to spot trends humans might miss. It can detect unusual energy spikes or signs that a machine might need maintenance.
3. Smart Recommendations or Actions
Once the AI system understands the patterns, it can act. It does this in two main ways:
A. Recommendations
AI can give suggestions to factory managers or facility teams, such as:
- Turning off specific machines during idle times.
- Adjusting HVAC settings when the weather changes or the building is empty.
- Rearranging production tasks to avoid peak electricity rates.
These recommendations help staff make better energy decisions without guessing.
B. Automatic Actions H3
In more advanced setups, AI can also control specific systems directly. It can:
- Automatically dim lights in areas that aren’t being used.
- Adjust heating or cooling based on occupancy or outside temperature.
- Reschedule machines to run during off-peak hours when electricity is cheaper.
This real-time automation is where AI shines. It allows factories to reduce energy use without slowing down production.
The Result
By using AI to collect data, learn from it, and act on it, factories can reduce waste, save money, and lower their carbon footprint. The process is continuous—AI keeps learning and improving as more data comes in. This means energy use becomes more innovative and efficient over time.
AI doesn’t just help solve energy problems. It helps prevent them before they start. AI-powered energy optimization is a wise investment for any modern manufacturing plant.
Getting Started: Steps for Manufacturers to Optimize Energy Using AI
AI-powered energy optimization is a smart place to start if you’re running a manufacturing facility and want to reduce energy costs, improve efficiency, and meet sustainability goals. Here’s a step-by-step guide to help you begin your journey simply and practically.
Step 1: Assess Current Energy Usage
Before jumping into AI solutions, you need to understand how energy is used in your factory. This means conducting a detailed energy audit. Start by identifying:
- Which machines consume the most power
- When energy demand peaks during the day or week
- Which areas (or shifts) are less efficient
- Common energy waste points, such as idle machines or unnecessary lighting
This assessment gives you a clear starting point and helps you prioritize which parts of your facility to focus on first.
Step 2: Install Smart Sensors and IoT Devices
Once you know where to look, it’s time to install smart sensors and IoT (Internet of Things) devices throughout your facility. These devices collect real-time data on:
- Power usage by each machine or system
- Temperature, humidity, and lighting conditions
- Equipment performance and run-time
- Occupancy levels in different zones
These sensors act like the eyes and ears of your energy system. They feed continuous, accurate data into your AI platform, allowing it to monitor operations 24/7 without human supervision.
Step 3: Choose the Right AI Platform
Many AI platforms are available for energy optimization, so choosing one that fits your factory’s size, complexity, and goals is essential. Look for platforms that offer:
- Real-time data analysis
- Predictive maintenance features
- Automated control of systems (like HVAC, lighting, or production lines)
- Easy integration with your existing infrastructure
Consider consulting with an AI vendor or energy consultant to ensure the platform meets your technical and budgetary needs.
Step 4: Run a Pilot Test
It’s a good idea to run a pilot test before rolling out the AI solution across the entire factory. Choose one production line, section, or facility zone to start with. This pilot phase will help you:
- Validate the accuracy of the data collected
- Measure energy savings and performance improvements.
- Identify any integration or technical issues early.y
- Train your team on how to use the system effectively
A successful pilot will build confidence in the technology and provide a roadmap for scaling up.
Step 5: Monitor, Learn, and Improve
AI systems get smarter over time. Once your system is live, monitoring its performance, allow it to learn from new data. The AI platform will continue to find new patterns, optimize energy usage more precisely, and make better decisions. Encourage your team to review AI insights regularly and apply recommended changes.
Also, remember to update goals and strategies as your operations grow or change. AI-powered energy optimization is not a one-time fix—it’s an ongoing improvement process that drives long-term value.
By following these five steps, manufacturers can smoothly transition toward smarter, greener, and more cost-efficient operations.
Final Thoughts
AI-powered energy optimization is no longer just a “nice-to-have”—a wise investment. It helps manufacturers reduce energy costs, improve operations, and become more eco-friendly. With fast ROI and long-term benefits, it’s a powerful way to future-proof your factory.