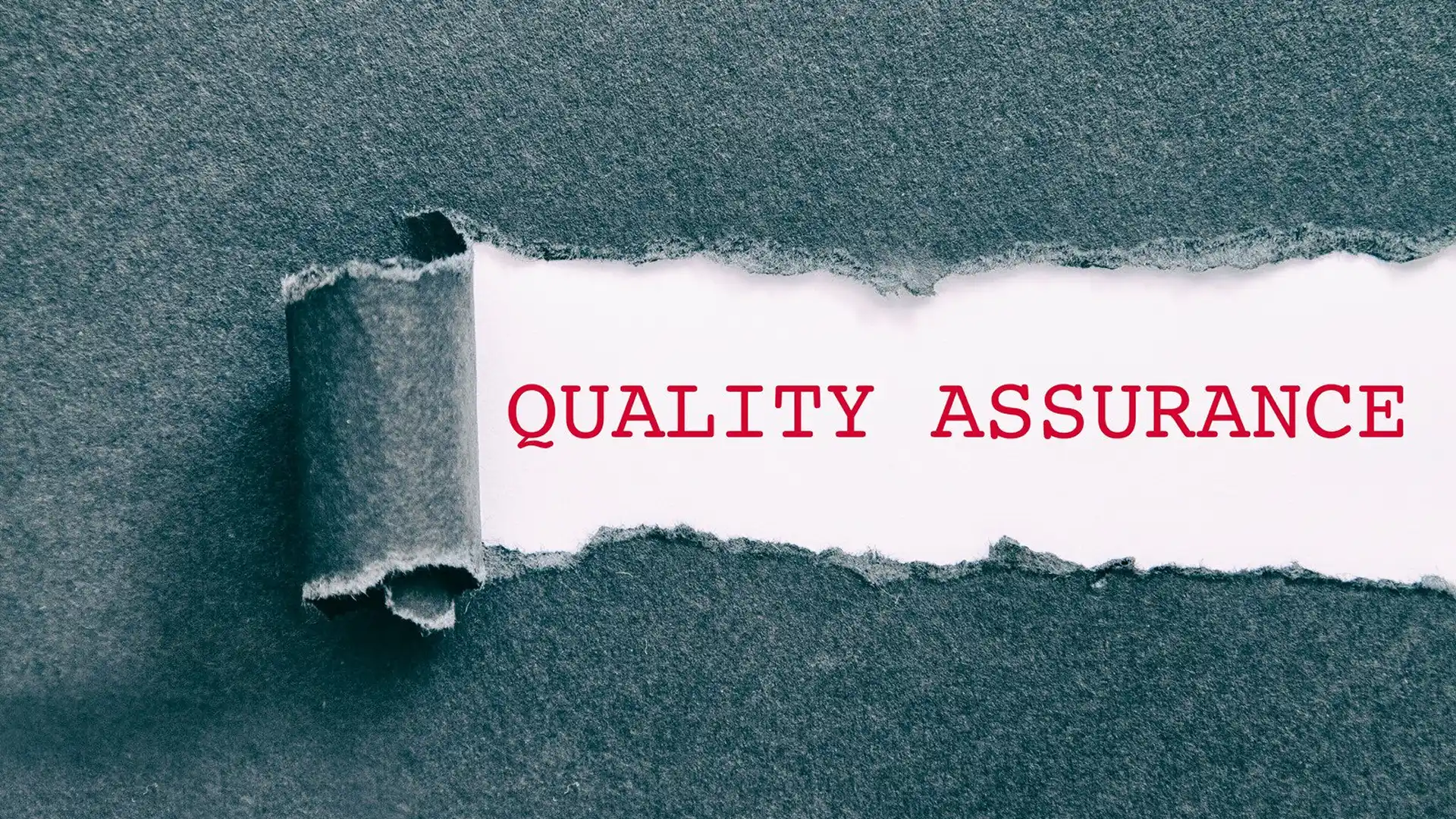
Key Takeaways
- Intelligent Automation combines AI, ML, and RPA with computer vision to transform traditional QA into faster, more accurate, and scalable inspection systems.
- Computer vision enables real-time, non-intrusive defect detection, pattern recognition, dimensional analysis, and label verification on production lines.
- IA-driven QA systems reduce human error, provide real-time feedback, and enable instant corrective actions, improving product quality and operational efficiency.
- Successful IA implementation requires pilot projects, collaboration with QA experts, modular, scalable systems, and investment in data annotation for training AI models.
- Continuous monitoring and retraining of AI models are vital to adapting to manufacturing changes and ensuring sustained inspection accuracy and compliance.
In today’s hyper-competitive manufacturing landscape, the demand for flawless products delivered at scale has never been higher. Quality Assurance is the backbone of production excellence, but traditional QA methods are increasingly falling short. Human inspectors, sampling methods, and manual defect detection struggle to keep pace with modern production lines’ speed, complexity, and customization demands.
Enter Intelligent Automation, particularly computer vision-based systems, which are revolutionizing how manufacturers approach QA. These technologies bring precision, speed, and consistency to quality checks, helping manufacturers maintain high standards while scaling operations efficiently.
This blog explores how computer vision is integrated into intelligent QA automation, its real-world applications, benefits, challenges, and the path forward.
Intelligent Automation in Quality Assurance
Intelligent Automation in Quality Assurance represents a significant advancement over traditional QA methodologies. It combines Artificial Intelligence, Machine Learning, and automation technologies such as Robotic Process Automation to enable more efficient, accurate, and scalable QA processes with minimal human intervention. In industries where product quality and consistency are critical, such as manufacturing, pharmaceuticals, automotive, and electronics, Intelligent Automation is transforming how QA is performed.
One of the most impactful applications of IA in QA involves using computer vision for automated visual inspection. High-resolution cameras and advanced sensors are strategically deployed along production lines to capture detailed images or videos of products as they are being manufactured. These visual data streams are then processed using AI and ML algorithms trained to recognize patterns, detect anomalies, and identify potential defects, such as surface imperfections, misalignments, incorrect labeling, or missing components.
Integrating AI/ML models enables the system to detect known issues and learn over time to identify new types of defects that may not have been explicitly programmed. This self-learning capability drastically enhances the adaptability and intelligence of QA systems, making them more resilient to product variations or changes in manufacturing conditions.
These intelligent systems rely on edge computing or cloud-based processing units for real-time performance. Edge computing processes data directly on or near the production site, enabling instant analysis and decision-making without the latency associated with cloud-based systems. However, in high-volume or multi-site environments, cloud infrastructure may be preferred for centralized model training, analytics, and remote monitoring.
Once a defect is detected, the IA system can automatically trigger a predefined response using control systems. These actions may include rejecting the defective item, halting the production line, notifying a quality supervisor, or adjusting machine parameters to prevent recurrence. This closed-loop control ensures faster response times and maintains consistent product quality without constant human oversight.
Beyond visual inspection, Intelligent Automation in QA can extend to other areas such as process monitoring, compliance verification, and test automation in software QA. When paired with predictive analytics, IA systems can forecast potential failures or deviations before they occur, further enhancing preventive quality control.
The Shift from Traditional QA to Intelligent Automation
Traditional QA Methods:
- Manual inspections by trained personnel
- Random sampling instead of full inspection
- Post-production quality checks
- High variability in results due to human error
- Slower feedback cycles
Intelligent QA with Computer Vision:
- Real-time, automated inspection of every product
- Non-intrusive, continuous monitoring across the line
- Instant detection and classification of defects
- Consistent, data-driven results
- Immediate response and feedback to production systems
This transition drastically improves operational efficiency, product quality, and customer satisfaction.
How Computer Vision Works in Manufacturing Quality Assurance?
Computer vision in manufacturing Quality Assurance is a transformative technology that enables automated visual inspection with precision, speed, and consistency. It simulates human visual perception but operates more efficiently, allowing manufacturers to maintain rigorous quality standards without sacrificing productivity. By integrating high-resolution imaging systems with advanced Artificial Intelligence (AI) and Machine Learning (ML) models, computer vision systems can detect and respond to product quality issues in real time, ensuring defect-free production at scale.
How does it work?
The process begins with image acquisition, where high-speed cameras and optical sensors are strategically installed along production lines to continuously capture images or video streams of the products being manufactured. Depending on the inspection requirements, these cameras may use various techniques, such as 2D imaging, 3D scanning, infrared, or X-ray.
Once the visual data is captured, it is sent to a processing unit, often equipped with edge computing or cloud-based resources. Here, sophisticated AI/ML algorithms analyze the images by comparing them against pre-trained models and quality benchmarks. These models are typically trained on vast datasets comprising acceptable and defective product images, enabling the system to recognize even subtle defects or deviations.
Key Capabilities of Computer Vision in QA
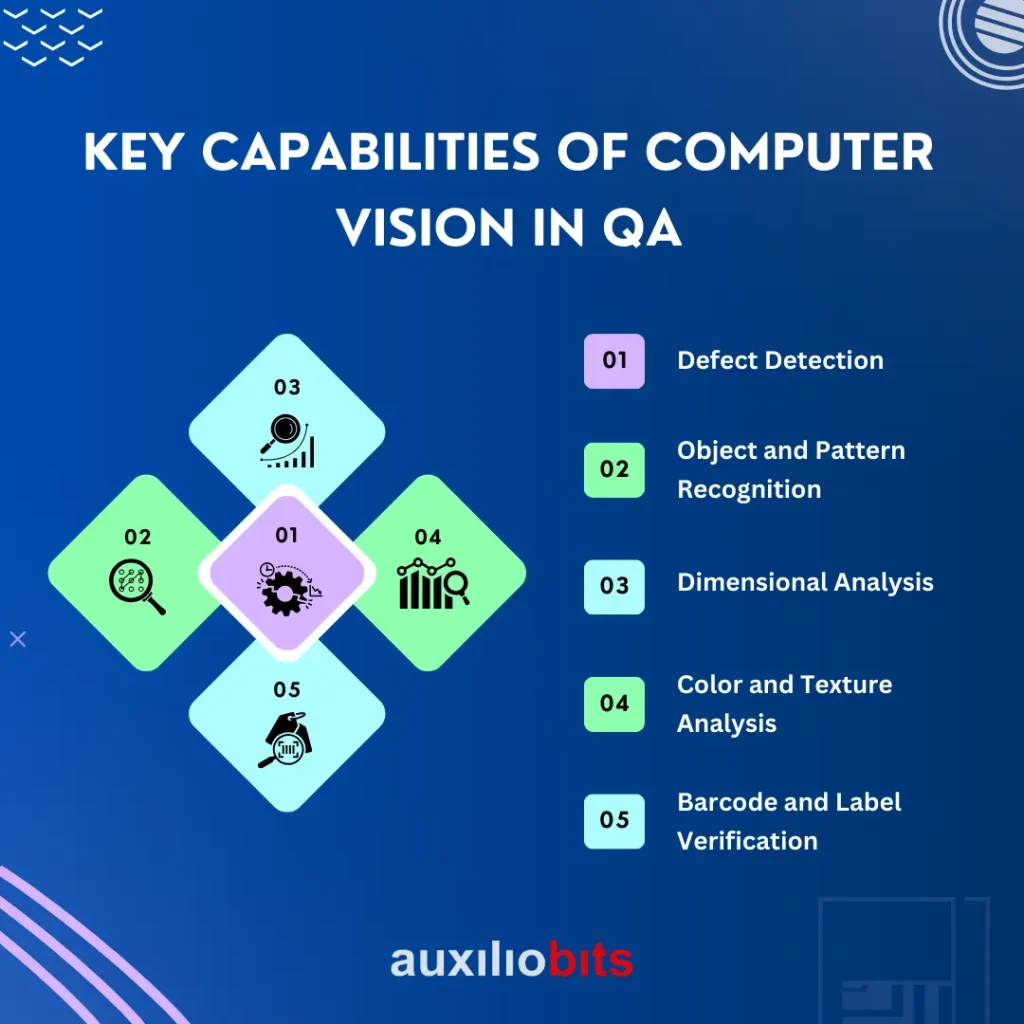
1. Defect Detection
The core function of computer vision in QA is the detection of physical defects such as scratches, dents, cracks, chips, smudges, stains, or any irregularities that may compromise product quality. The system flags these defects accurately, allowing for real-time rejection or remediation.
2. Object and Pattern Recognition
Computer vision systems can verify whether all necessary components are present and correctly assembled. For instance, in automotive or electronics manufacturing, the system checks for correct placement, orientation, or rotation of parts like screws, chips, or connectors. Pattern recognition capabilities also help ensure that logos, labels, and designs are correctly printed and aligned.
3. Dimensional Analysis
Precise measurements are critical in high-tolerance industries. Computer vision can measure distances, angles, gaps, and sizes to validate whether the product dimensions are within acceptable tolerances. This eliminates the need for manual caliper checks and speeds up QA processes.
4. Color and Texture Analysis
Uniformity in color, glossiness, texture, and surface finish is essential, particularly in consumer-facing products. The system can detect color mismatches, surface roughness, or inconsistent finishes that human inspectors might otherwise overlook.
5. Barcode and Label Verification
Computer vision ensures that every product is correctly labeled with barcodes, QR codes, expiry dates, serial numbers, or batch information, essential for compliance, traceability, and logistics. OCR (Optical Character Recognition) techniques allow these elements to be validated instantly.
Real-Time and Non-Disruptive
One of the most significant advantages of computer vision in QA is its non-intrusive and real-time operation. Inspections occur in milliseconds and are synchronized with the production line’s movement, ensuring no bottleneck or disruption to throughput. This continuous, automated monitoring reduces the reliance on manual inspections, which are slower, more error-prone, and unsustainable at high volumes.
Modern systems offer scalability and adaptability, enabling manufacturers to rapidly reconfigure inspection parameters for new products or evolving quality standards. Integration with control systems means detected issues can trigger automated responses, such as product rejection, machine recalibration, or alerts to a human operator, thus enabling a closed-loop QA system.
Technical Architecture of a Vision-Based QA System
A typical intelligent QA system using computer vision includes:
Component | Role |
Industrial Cameras | Capture high-resolution images or video of products in motion |
Lighting Setup | Ensures consistent and shadow-free visuals for accurate analysis |
Edge Processing Units | Analyze visual data locally to reduce latency |
AI/ML Models | Detect defects, measure dimensions, and classify issues |
Dashboard/Interface | Displays results, analytics, and insights for operators |
Integration Layer | Connects to MES, ERP, or PLC systems to automate corrective action |
Benefits of Intelligent Automation in Quality Assurance
Intelligent Automation is revolutionizing Quality Assurance by combining artificial intelligence, machine learning, and robotic process automation with real-time visual inspection technologies. This convergence brings tangible benefits that enhance QA’s efficiency and effectiveness in modern manufacturing and production environments. Here’s a detailed look at the key advantages:
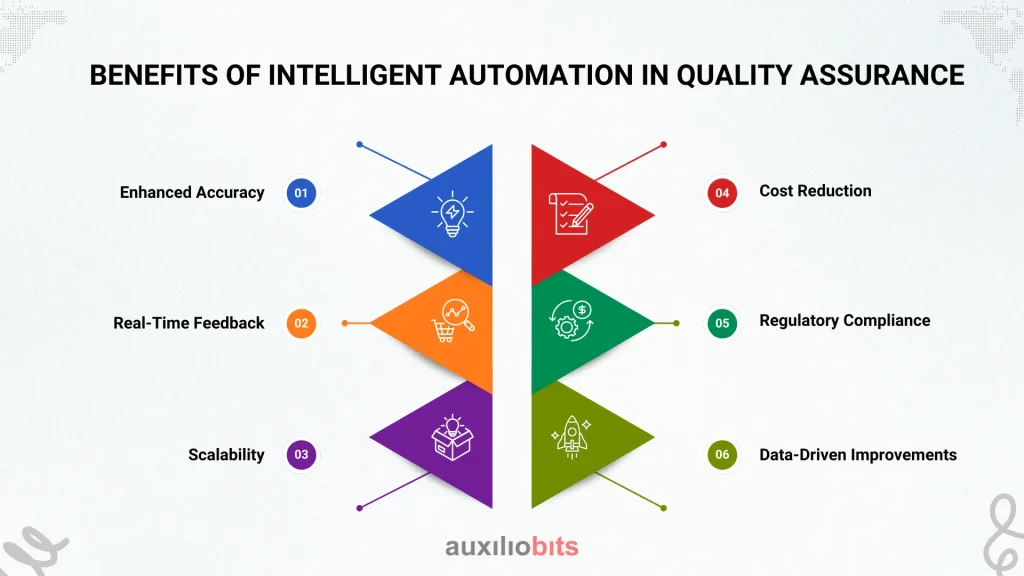
1. Enhanced Accuracy
One of the most significant benefits of intelligent automation in QA is unmatched inspection accuracy. Traditional manual inspections are prone to human error, fatigue, and inconsistency, especially in high-volume or high-speed environments. In contrast, AI-powered systems can be trained on vast datasets containing images of defective and defect-free products. These models learn to detect even the most minute imperfections—such as hairline cracks, microscopic dents, or barely visible misalignments—with precision and consistency. This reduces false positives (flagging non-defective products) and false negatives (missing actual defects), ensuring higher product quality and fewer customer complaints.
2. Real-Time Feedback
Unlike traditional QA methods that rely on post-production sampling and batch testing, intelligent automation enables real-time inspection and feedback. As products move through the production line, computer vision systems immediately analyze them and flag any defects or deviations from quality standards. This allows operators and control systems to make instant corrections, such as rejecting a defective item, adjusting equipment settings, or pausing the line to prevent further issues. Real-time feedback dramatically reduces material waste, rework costs, and the chances of defective products reaching customers.
3. Scalability
Another key advantage is the scalability of automated QA systems. Once deployed, these systems can operate 24/7 without fatigue or degradation in performance. They can inspect thousands of units per hour with the same level of attention and detail—something impossible for human inspectors. This makes intelligent automation ideal for high-throughput industries like automotive, electronics, pharmaceuticals, and consumer goods manufacturing. As production demands grow, additional vision systems and processing units can be added with minimal disruption.
4. Cost Reduction
While the initial investment in IA technology can be significant, the long-term cost savings are substantial. Automation reduces the need for large teams of manual inspectors, lowers scrap rates by catching defects early, and minimizes product recalls caused by undetected quality issues. Additionally, fewer human errors translate into fewer warranty claims and less reputational damage. Over time, companies achieve a high return on investment (ROI) through improved efficiency, reduced waste, and higher customer satisfaction.
5. Regulatory Compliance
Industries such as pharmaceuticals, aerospace, and automotive are subject to strict regulatory requirements regarding product quality and traceability. Intelligent automation facilitates compliance by automatically capturing and storing detailed inspection data, including high-resolution images of defects, timestamps, and decision logs. This digital documentation streamlines audit processes, simplifies regulatory reporting, and ensures that companies meet the standards set by organizations like the FDA, ISO, or NHTSA.
6. Data-Driven Improvements
inspection creates data that can be aggregated and analyzed to identify trends, recurring defects, or bottlenecks in the production process. By using this data for root cause analysis and predictive maintenance, manufacturers can proactively address issues before they escalate. Over time, these insights enable continuous improvement in product quality, equipment performance, and overall operational efficiency.
Best Practices for Implementing Intelligent Automation in Quality Assurance
Implementing Intelligent Automation in Quality Assurance can dramatically improve manufacturing outcomes, but a successful rollout requires careful planning and execution. Manufacturers must adopt best practices that mitigate risks, optimize resource utilization, and ensure the technology delivers measurable value. Here are detailed best practices to guide organizations through a smooth and effective implementation:
1. Start with a Pilot Project on a High-Impact Production Line
One of the most critical steps in implementing IA for QA is to begin with a pilot project rather than a full-scale rollout. Select a production line or process that highly impacts product quality, operational efficiency, or cost savings. This approach allows the organization to validate the technology’s effectiveness on a manageable scale, identify unforeseen challenges, and demonstrate clear ROI before expanding.
A pilot project also provides valuable real-world data and feedback that can be used to fine-tune AI models, adjust workflows, and train staff. Choosing a high-impact area ensures that even a limited deployment can generate significant benefits and build stakeholder confidence.
2. Involve Process Engineers and QA Experts Early
Collaboration with process engineers and QA experts is essential to define clear and precise defect criteria and quality standards. These professionals understand the nuances of the manufacturing process and what constitutes an acceptable or unacceptable product. Their input is crucial for:
- Designing inspection parameters
- Labeling data accurately for training AI models
- Interpreting the system’s outputs and making informed decisions
- Setting realistic performance benchmarks
Engaging them early also helps to align the automation system with existing quality protocols and facilitates user buy-in, which is key to successful adoption.
3. Use Modular, Scalable, and Integrable Systems
Implementing a modular IA system that can scale horizontally and vertically is a best practice supporting current needs and future growth. Modular solutions allow manufacturers to start small and incrementally add new inspection stations, sensors, or AI capabilities without major overhauls.
Furthermore, the chosen system should be easily integrable with existing production equipment, enterprise resource planning (ERP), manufacturing execution systems (MES), and quality management systems (QMS). Seamless integration reduces implementation complexity and helps automate workflows, from defect detection to reporting and corrective action.
4. Invest in Data Annotation Tools or Partnerships for Faster Model Training
AI models rely heavily on high-quality, well-annotated training data for accurate defect detection. Manually annotating images and videos can be time-consuming and labor-intensive, often becoming a bottleneck during deployment.
Manufacturers should invest in specialized data annotation tools that facilitate rapid and consistent labeling or consider partnerships with external experts specializing in data preparation. This investment accelerates the training process and improves model accuracy, ultimately reducing time to value.
5. Regularly Monitor and Retrain AI Models to Adapt to Production Changes
Manufacturing environments are dynamic—raw materials, machines, and processes may evolve. AI models that perform well initially may degrade in accuracy if not appropriately maintained.
To sustain performance, manufacturers should establish a routine to monitor model outputs and system performance continuously. Collecting feedback on false positives or missed defects enables timely interventions. Regularly retraining AI models with new data reflecting current production conditions helps the system adapt to subtle changes, maintain reliability, and avoid costly quality lapses.
Conclusion
Intelligent automation is no longer a futuristic concept—it’s a present-day necessity in manufacturing QA. By harnessing the power of computer vision, manufacturers can transition from slow, error-prone inspections to precise, scalable, and data-driven quality control systems.
The result? Higher product quality, faster time to market, reduced operational costs, and a future-ready production line.