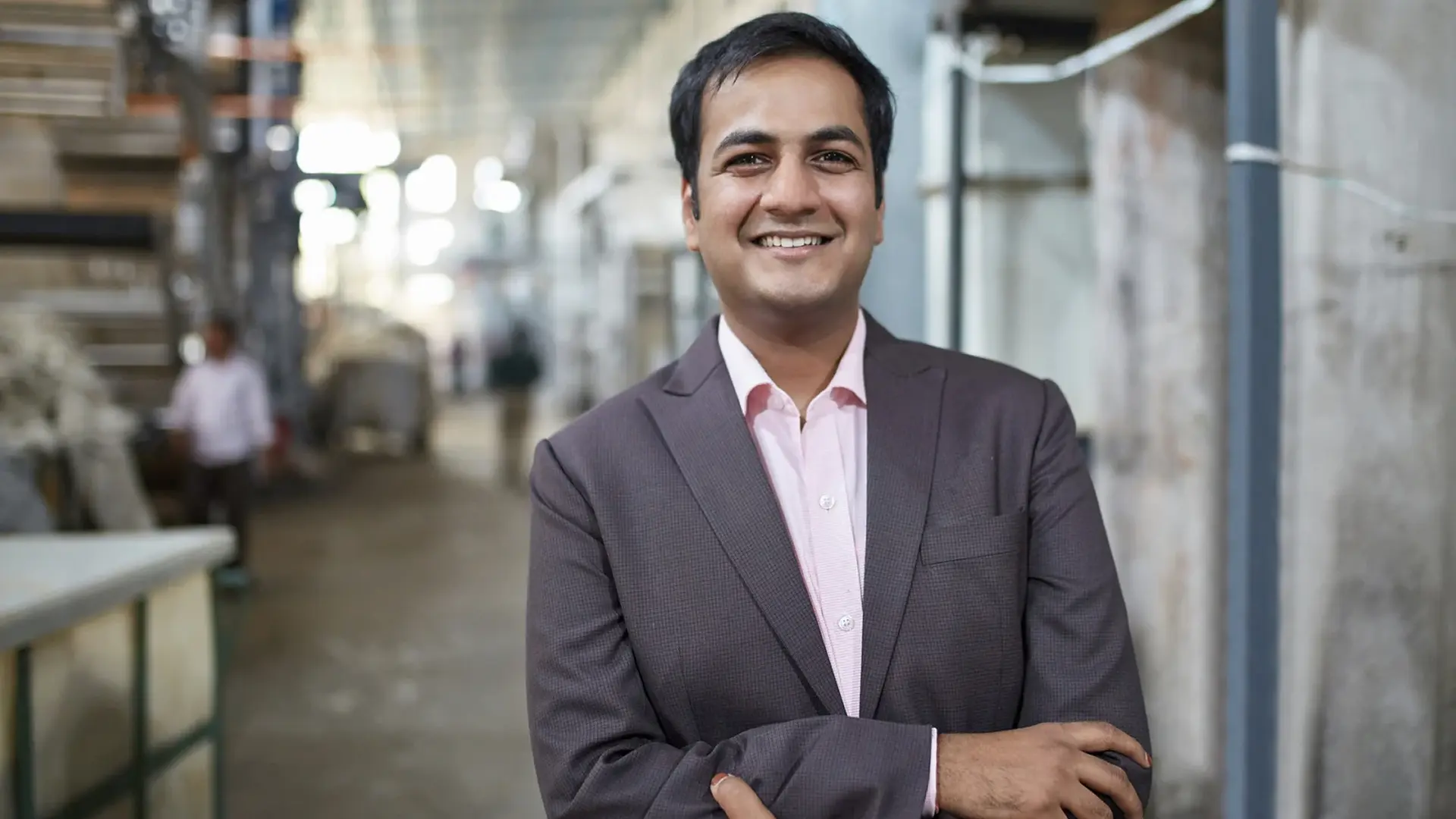
Key Takeaways
- Combining RPA, AI, and process mining streamlines manufacturing by automating tasks, optimizing decisions, and revealing inefficiencies, driving productivity and operational excellence.
- HyperAutomation empowers manufacturers to adapt swiftly to market demands, overcome labor shortages, and ensure compliance through intelligent, data-driven automation across all business functions.
- Begin automation with simple, repetitive tasks using RPA, then enhance with AI and expand organization-wide using insights from process mining for scalable digital transformation.
- AI analyzes real-time data to predict outcomes, such as equipment failures and demand changes, enabling proactive and informed decision-making and reducing downtime and product quality issues.
- HyperAutomation isn’t static—use process mining to continuously monitor performance, identify new automation opportunities, and adapt to evolving business challenges for sustained improvement.
The manufacturing industry is both competitive and complex. Several firms are competing with one another by offering unique services. Nevertheless, they need to keep in mind that manufacturers need to do more than just enhance their production lines. It is pivotal to consider how the operations are running. Therefore, this is where the combination of technologies, such as RPA and artificial intelligence, can make all the difference. Additionally, tools like process mining can also be beneficial.
Robotic process automation helps automate repetitive tasks, such as data entry and other manual processes. It is beneficial since these jobs require a significant amount of time and are prone to errors made by humans. RPA bots and software are capable of handling such duties, freeing manufacturers to concentrate on more critical ones. Conversely, artificial intelligence stimulates creative commercial processes. It also helps manufacturers to understand if there are any equipment failures. As a result, they can avoid delays and purchase new equipment if needed.
On the other hand, process mining is a tool that monitors how business processes operate in real-life situations. It helps manufacturers gather all the crucial details from current systems to identify any severe challenges. When robotic process automation, artificial intelligence, and process mining function together, they develop a robust system that helps enhance the manufacturing sector.
Also read: AI Strategy for Predictive Fleet Maintenance in Logistics.
What is HyperAutomation?
HyperAutomation is an advanced technique that manufacturers can utilize to streamline business procedures. Nevertheless, the benefits can be more fully enjoyed when combined with several complementary technologies. The primary objective of hyperautomation is to automate complex workflows and business processes. In comparison to standard automation, hyperautomation helps boost production and increase efficiency. It also makes operations smooth and agile.
Why Does Manufacturing Need HyperAutomation?
Manufacturers today face a range of challenges that can impact their ability to remain competitive. These challenges include rising labor costs, intense global competition, supply chain disruptions, quality control issues, and complex compliance requirements. To overcome these obstacles, manufacturers must become more agile, efficient, and data-driven. This is where HyperAutomation comes into play.
HyperAutomation enables manufacturers to automate routine and repetitive tasks, such as data entry, inventory tracking, and scheduling. By doing so, it frees up human workers to focus on more strategic activities that require creativity and problem-solving. Robotic Process Automation (RPA) handles these mundane tasks, reducing labor costs and improving efficiency.
Moreover, Process Mining enables manufacturers to analyze their processes in real-time, identifying inefficiencies, bottlenecks, and areas for improvement. This data-driven approach allows companies to make faster, more informed decisions, ultimately improving productivity and reducing costs.
Additionally, Artificial Intelligence (AI) enhances decision-making by using data to predict outcomes, such as equipment failures or changes in customer demand. By leveraging AI, manufacturers can optimize production schedules, prevent delays, and ensure the production of high-quality products with fewer errors.
Role of RPA in Manufacturing
RPA uses bots to handle repetitive tasks that are time-consuming for humans. In manufacturing, RPA can be used in areas like:
Use Case | Description |
Inventory Management | Bots update stock levels and generate purchase orders. |
Invoice Processing | Automates the scanning, matching, and approval of invoices. |
Order Management | Processes customer orders and updates systems automatically |
Data Entry | Transfers data between systems without errors. |
Compliance Reporting | Generates reports for audits and regulations. |
Role of AI in Manufacturing
AI adds intelligence to automation. Instead of just following rules, AI can learn from data and make wise decisions. Here are a few ways AI is used in manufacturing:
Use Case | Description |
Predictive Maintenance | AI analyzes machine data to predict breakdowns. |
Quality Control | Uses image recognition to spot defects in products. |
Demand Forecasting | Predicts future demand based on past sales and trends. |
Supply Chain Optimization | Suggests the best suppliers and routes. |
Chatbots for Support | Helps with internal queries and supplier communication. |
Role of Process Mining in Manufacturing
Process mining enables companies to gain a clear understanding of how their processes operate by analyzing event logs and system data. It helps answer questions like:
- Where are the delays?
- Which steps take the longest?
- Are there any unnecessary steps?
Use Case | Description |
Workflow Analysis | Finds bottlenecks in production and logistics. |
Process Optimization | Suggests ways to make workflows faster and smoother. |
Compliance Checking | Ensures that processes comply with internal and external regulations. |
Performance Monitoring | Tracks KPIs in real time. |
Benefits of Integrating RPA, AI, and Process Mining
Integrating Robotic Process Automation (RPA), Artificial Intelligence (AI), and Process Mining creates a robust automation framework that can significantly enhance manufacturing operations. When these three technologies work together, they provide unique strengths that complement each other, driving efficiency and improving overall performance. Here’s a breakdown of how each technology contributes to manufacturing success:
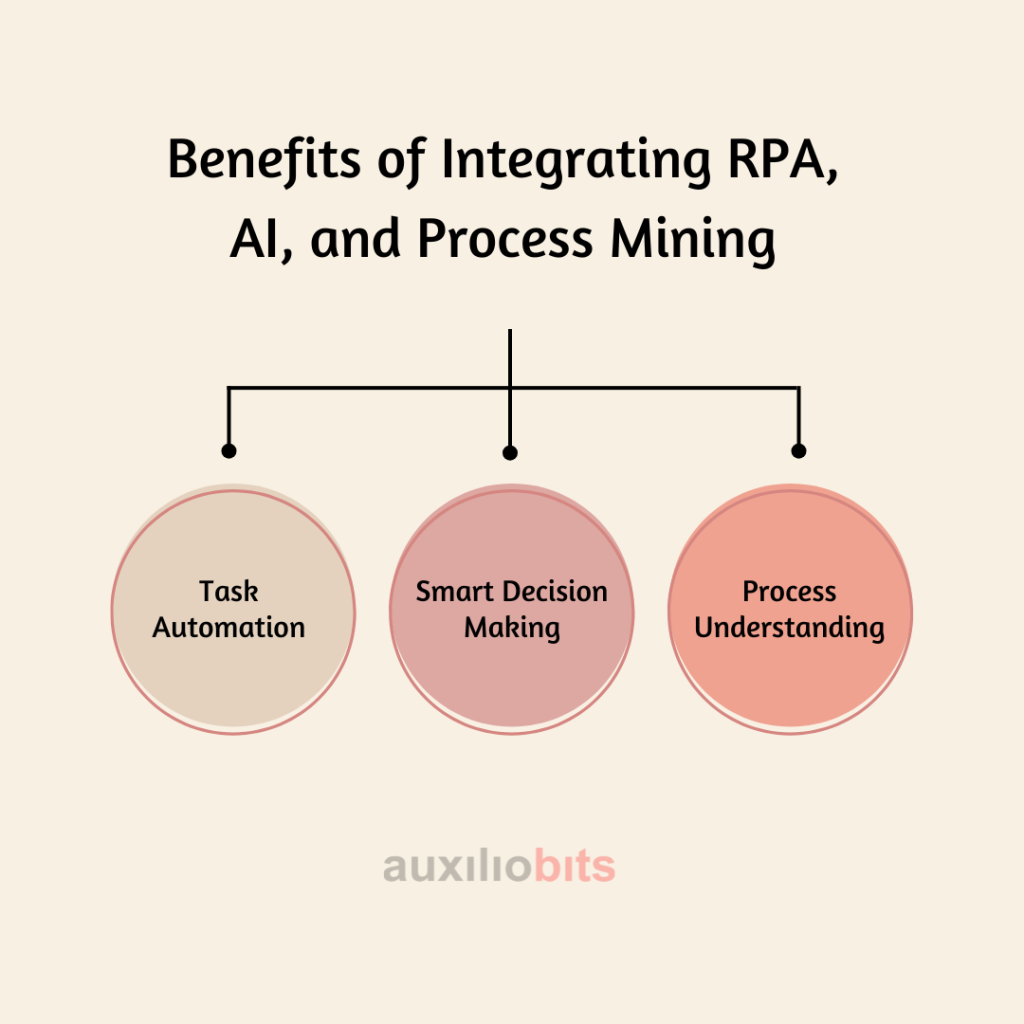
1. Task Automation
RPA excels in automating repetitive, rule-based tasks that are time-consuming and prone to human error. These tasks could include data entry, order processing, inventory updates, and generating reports. By automating these processes, RPA reduces manual labor, accelerates operations, and minimizes errors. As a result, manufacturers can free up valuable human resources to focus on higher-value activities, such as problem-solving, innovation, and strategy development. With RPA, manufacturers also achieve scalability, as bots can efficiently handle large volumes of tasks without requiring additional labor.
2. Smart Decision Making
AI adds a layer of intelligence to the automation process. It can analyze large volumes of data, recognize patterns, and make data-driven decisions in real time. In manufacturing, AI can optimize production schedules, predict equipment failures before they occur, and enhance product design through data-driven analysis. AI enables manufacturers to make more informed decisions by providing valuable insights that improve accuracy, minimize waste, and increase productivity. By analyzing trends and data points that may not be readily apparent to humans, AI can guide manufacturers in enhancing processes, forecasting demand, and tailoring production strategies.
3. Process Understanding
Process mining provides a detailed, real-time view of how manufacturing processes are functioning. By extracting data from enterprise systems, such as ERP or CRM systems, it visualizes the flow of tasks and identifies inefficiencies, bottlenecks, or deviations from optimal workflows. Manufacturers can utilize process mining to identify areas where processes are slow, errors occur, or resources are being wasted. This transparency enables them to streamline operations, improve process designs, and enhance overall performance. Process mining not only helps identify problems but also suggests opportunities for automation, enabling manufacturers to optimize their operations continuously.
Together, RPA, AI, and Process Mining help manufacturers:
1. Reduce Operational Costs
By automating repetitive tasks with RPA and improving decision-making with AI, manufacturers can reduce labor costs, minimize errors, and optimize resource use. Process mining helps identify inefficiencies, leading to further cost reductions.
2. Improve Product Quality
AI’s ability to analyze data ensures that production processes are optimized for high-quality outputs. RPA reduces human error, which can lead to defects, and process mining helps maintain consistency and quality by identifying process flaws early.
3. Increase Production Speed
Automation through RPA speeds up repetitive tasks, AI optimizes decision-making for faster adjustments, and process mining identifies slowdowns or bottlenecks, enabling manufacturers to take corrective action promptly.
4. Boost Worker Productivity
By automating routine tasks, workers can focus on higher-level work that requires creativity and problem-solving. AI can assist workers in making better decisions, while process mining ensures that operations run smoothly.
5. Stay Compliant with Regulations
Manufacturing industries often have strict compliance requirements. AI can help monitor compliance by analyzing data and ensuring that all regulations are met. RPA ensures that routine tasks are completed according to regulatory standards, and process mining can help track adherence to processes that meet industry regulations.
How to Get Started with HyperAutomation?
Implementing hyperautomation in your organization requires a structured approach. By following these steps, you can build a solid foundation and scale automation across your business.
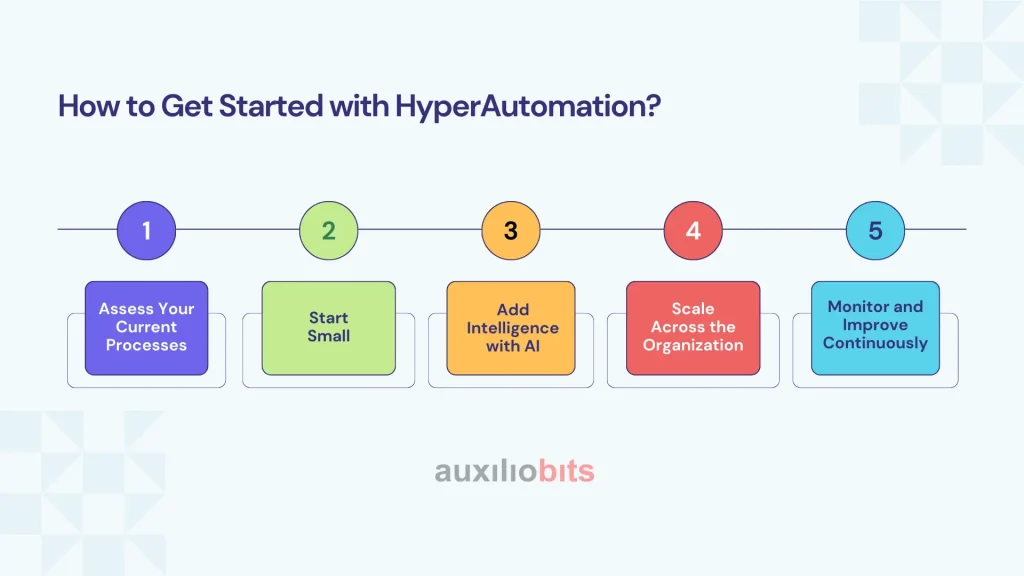
1. Assess Your Current Processes
The first step in adopting hyperautomation is to assess your current business processes. Process Mining tools are essential here, as they provide an in-depth view of how your workflows are operating in real time. These tools help you identify inefficiencies, bottlenecks, and areas that require improvement. By analyzing data from your existing systems, such as ERP or CRM, you can pinpoint where automation can have the most significant impact.
2. Start Small
Once you’ve identified a process that can benefit from automation, start by implementing it on a small scale. Select a repetitive, rules-based task, such as data entry or report generation, that can be easily automated using robotic process automation (RPA). This will allow you to see the benefits of automation quickly and with minimal risk. By automating a simple task first, you can gain valuable insights into the technology and understand how it fits within your organization’s overall framework.
3. Add Intelligence with AI
After successfully implementing RPA, you can take your automation to the next level by adding artificial intelligence. AI can analyze data, recognize patterns, and make intelligent decisions in real time. For instance, AI can help predict demand fluctuations, optimize inventory management, or improve production scheduling. With AI in place, your automation becomes more intelligent and more adaptive, providing greater value to your business.
4. Scale Across the Organization
Once you’ve seen success with RPA and AI in one area, expand automation to other departments. Logistics, finance, customer service, and HR are all areas that can benefit from HyperAutomation. By applying automation across departments, you can streamline processes and improve efficiency throughout the entire organization.
5. Monitor and Improve Continuously
Hyperautomation is not a one-time effort. Use Process Mining to continuously monitor performance and track improvements. This allows you to identify new opportunities for automation and optimization. By regularly assessing the performance of automated processes, you can ensure that your business remains agile and can adapt to changing conditions.
The Closing Thoughts
Hyperautomation is a practical approach to making manufacturing smarter, faster, and more efficient. By combining RPA, AI, and process mining, companies can unlock new levels of productivity and quality. Whether you’re looking to reduce costs, improve workflows, or stay ahead of competitors, integrating these technologies is a step in the right direction.
Start small, learn as you go, and scale your automation strategy over time. The future of manufacturing is intelligent, and it starts with hyperautomation